Stade de France, Paris, France. 3 août 2024. 22h30. « À vos marques ! » Il est fascinant de voir à quel point une foule de 80 000 personnes peut se calmer en quelques secondes. Vous pourriez entendre les mouches voler s’il n’y avait pas les voix étouffées des journalistes de télévision et de radio dans la tribune presse et les neuf corps musclés prenant lentement position, accroupis, dans les starting-blocks. Les dix prochaines secondes détermineront si les années d’efforts porteront leurs fruits, s’ils saisiront l’opportunité unique qui leur est offerte d’accéder à la gloire olympique. « Prêts ? »
Pour en arriver là, ces athlètes ont dû prêter attention à chaque détail avec peu de marge d’erreur. Des milliers d’heures sur la piste. Des millions de kilos levés à la salle de sport. Des centaines de séances douloureuses chez le kiné. Des horaires stricts et méticuleux pour tous les aspects de la vie, des habitudes de sommeil à la nutrition. Sans parler de l’équipement : outre les vêtements de course parfaitement ajustés, il a fallu tester des dizaines de paires de chaussures à pointes, si légères qu’elles sont à peine perceptibles mais offrant tout de même une transmission de puissance maximale au départ de la course. Tout cela dans l’espoir que l’effort sera payant, que la machinerie humaine ne sera pas entravée et fonctionnera à pleine capacité lorsque le moment sera venu.
Il existe un autre domaine dans lequel le poids et l’attention portée aux détails jouent un rôle tout aussi important : les voitures. Au fil des ans, elles sont devenues des athlètes de haut niveau en développant des « muscles » automobiles, mais au prix d’une masse accrue. Et comme les régulateurs, tels que l’Union Européenne, obligent les équipementiers à réduire l’empreinte carbone de l’ensemble de leurs flottes, ils cherchent à leur tour des moyens d’optimiser la configuration de leurs meilleurs athlètes, une pièce allégée à la fois. C’est là qu’interviennent les entraîneurs Continental.
Un partenariat avec des experts en matériaux légers
Nos experts en allègement automobile sont basés à Rennes en France. Il y a dix ans, ils ont commencé à chercher des moyens de développer des pièces allégées qui fonctionneraient tout aussi bien que les solutions traditionnelles, et ont trouvé une approche possible dans l’industrie aéronautique. Dans ce secteur, les ingénieurs utilisent depuis longtemps des composites avec des fibres continues pour de réaliser des pièces aux grandes dimensions. Pourquoi cette méthode ne pourrait-elle pas également constituer une solution pour les applications automobiles ?
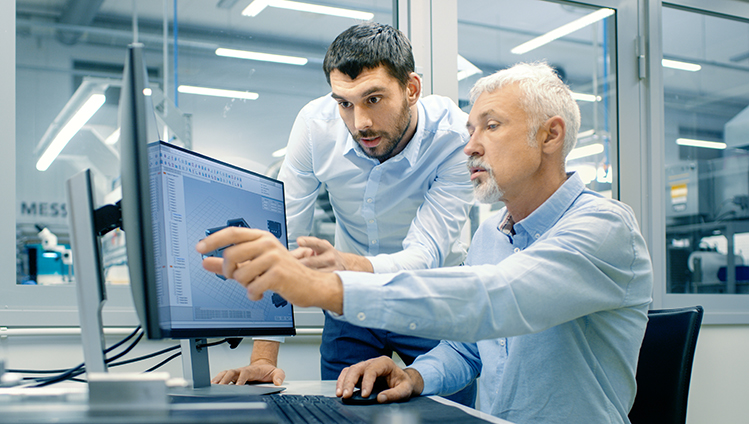
Ainsi, ils se sont associés à d’autres pionniers dans le domaine des matériaux légers pour combiner leur expertise dans les systèmes anti-vibrations, le caoutchouc et les thermoplastiques avec le savoir-faire de l’industrie aéronautique dans les composites thermoplastiques et les processus automatisés de placement de fibres. Ajoutez-y le fruit des recherches les plus récentes de deux universités, et voilà : vous obtenez Dynafib, une nouvelle solution matérielle pour les pièces automobiles.
Des pièces solides avec moins de masse : Dynafib favorise la perte de poids automobile
Dynafib est une technologie légère et se compose de plusieurs couches de tape en boucle fermée. Le tape est constitué de plusieurs centaines de fibres de verre très longues, toutes alignées dans la même direction, qui sont imprégnées dans une matrice thermoplastique. Les couches sont ensuite fusionnées à l’aide d’un faisceau laser. Plus une pièce devra être solide et robuste, plus le nombre de couches sera important. C’est pourquoi la technologie Dynafib est particulièrement adaptée aux pièces qui doivent supporter des charges internes dirigées vers l’extérieur, comme les biellettes de reprise de couple.
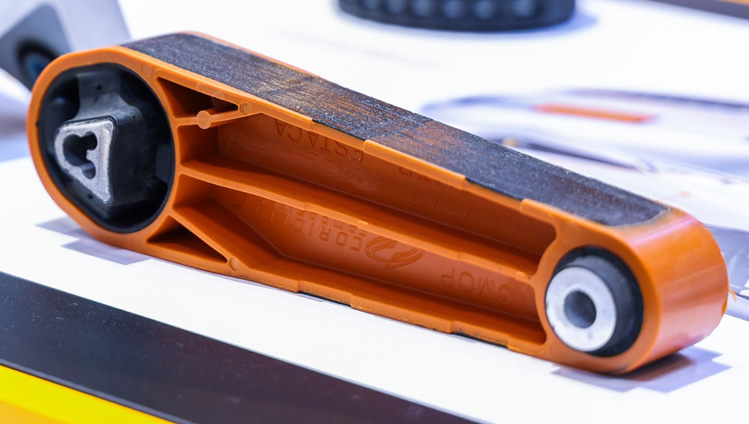
Ces dernières représentent l’exemple parfait pour examiner de plus près le potentiel de Dynafib pour réduire le poids tout en maintenant les performances. Les biellettes de reprise de couple sont généralement en acier ou en aluminium et atténuent l’impact du couple moteur dans un véhicule en empêchant le transfert de vibrations et de bruit, ainsi qu’en limitant le roulis du moteur. Afin de relier en toute sécurité l’ensemble des pièces du composant, le renfort Dynafib est combiné aux deux articulations caoutchouc, grâce au surmoulage d’un polyamide, assurant ainsi la fonctionnalité structurelle de la pièce. Comme le renfort Dynafib a été conçu spécifiquement à cette fin, il empêche la biellette de reprise de couple de se casser en deux et améliore considérablement sa résistance pour un poids bien moindre.
Mais à quel point ? Prenons une biellette de reprise de couple en aluminium comme référence pour notre comparaison. Une biellette en acier de même résistance serait environ 20 % plus lourde. Une biellette de reprise de couple en thermoplastique non renforcée pèse environ 75 % du poids d’une barre en aluminium, mais assure seulement 50 % de sa résistance. Seule la solution légère Dynafib atteint les mêmes valeurs de résistance que les versions métalliques, tout en réduisant la masse d’environ 50 % par rapport à l’aluminium.
Défis rencontrés lors du développement de nouvelles technologies légères
Bien que Dynafib soit une technologie hautement innovante, elle ne convient malheureusement pas à toutes les applications ou à tous les composants automobiles. En général, seules les pièces pouvant être renforcées à l’aide d’une seule bande droite peuvent être améliorées, puisque la bande Dynafib ne peut pas être tordue. De plus, il a fallu mettre au point un processus de production pour assurer que tous les composants étaient correctement assemblés en optimisant l’injection thermoplastique.
La taille du composant représente également un défi. Depuis de nombreuses années, les acteurs de l’industrie aéronautique réalisent de grandes surfaces aux courbes arrondies en utilisant plusieurs couches de tape drapées dans plusieurs directions. Cependant, la production d’un si grand composant léger prend beaucoup de temps. Et le temps est un facteur critique, car c’est l’une des principales exigences de l’industrie automobile, avec les coûts, lors du développement de pièces. Par conséquent, le nombre de pièces à produire à faible coût est bien supérieur à celui d’un cockpit d’avion. en effet, pour assurer la rentabilité, les biellettes Dynafib doivent être produites à une vitesse élevée de 20 à 30 secondes par unité.
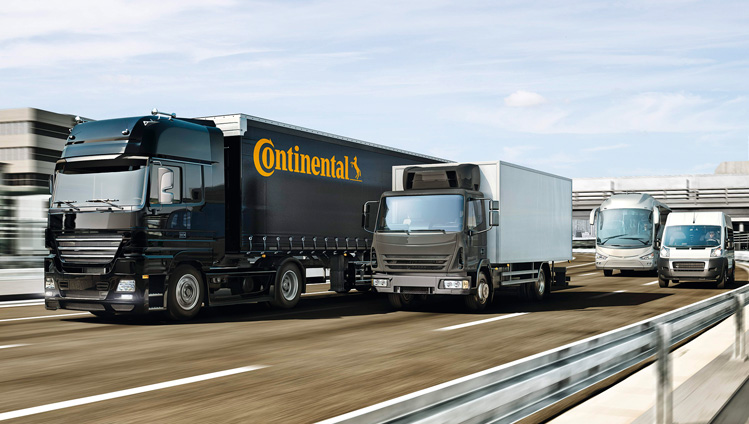
Il y a donc beaucoup d’éléments à considérer si vous souhaitez passer d’une pièce métallique standardisée à de nouvelles technologies légères. Cependant, alors que la biellette Dynafib de Continental entrera en production en série au printemps, nos experts matériaux et produits de Rennes travaillent déjà sur la manière d’alléger d’autres composants automobiles tels que les bras de liaison et les membranes à air, pour lesquels nous espérons économiser environ un tiers de leur poids initial grâce à l’application de Dynafib.
Et si les entraîneurs Dynafib se concentraient jusqu’à présent sur les voitures, ils se penchent déjà sur le reste du monde, convaincus qu’il existe également d’autres véhicules qui gagneraient à perdre du poids : camions, véhicules agricoles, engins de chantier, tramways et trains, vélos et autres mobilités douces. Sans parler des autres applications industrielles en dehors de la mobilité, l’éventail des possibilités de solutions légères est presque aussi large que le nombre d’événements de cet été magique de 2024 qui se dérouleront dans la capitale française.
L’avenir : des solutions légères durables
Perdre du poids n’est évidemment pas une fin en soi, ni pour les athlètes, ni pour les voitures. Pour les équipementiers, l’exercice a un but : le développement durable. Un véhicule plus léger entraîne une consommation de carburant réduite et donc moins d’émissions de CO2. Mais chez Continental, nous ne regardons pas seulement la chaîne de valeur en aval, nous regardons aussi nos propres matériaux, solutions et processus. Ce qui est incroyable avec Dynafib, c’est que le processus de production lui-même ne consomme pas beaucoup d’énergie. Néanmoins, son empreinte carbone globale n’est pas encore à la hauteur de nos espérances, principalement en raison des matériaux utilisés : la fibre de verre et les matériaux thermoplastiques.
Nos experts Dynafib à Rennes y travaillent également. Ils espèrent que dans deux ans, ils pourront introduire une nouvelle solution légère utilisant la technologie Dynafib avec des matériaux biosourcés et des polymères recyclés, ce qui réduirait l’empreinte carbone globale à seulement une fraction de son niveau actuel. Un vrai poids plume à pleine puissance. Et d’ici là, peut-être que certains d’entre eux feront partie de ces 80 000 fans qui acclameront lorsque le coup d’envoi retentira à Paris. « Partez ! »